Key Advantages of Utilizing Plastic Injection Molding in Manufacturing
Plastic injection molding has emerged as a critical method in the manufacturing sector, providing a variety of advantages that dramatically boost manufacturing procedures. Significant advantages consist of impressive manufacturing performance, the capability for complex layouts, and a positive expense structure that allures to businesses of all sizes.
High Manufacturing Effectiveness
One of the most significant benefits of plastic shot molding is its high production efficiency, which can result in the rapid manufacturing of thousands of similar components within a brief timeframe. This effectiveness is greatly associated to the automated nature of the shot molding procedure. When the first setup and mold production are finished, the manufacturing of parts can be scaled up significantly without a corresponding boost in labor expenses or time.
The process commonly involves heating plastic pellets up until they melt, injecting the molten material into a specifically developed mold, and enabling it to cool and strengthen - Plastic Injection Molding. This cycle can be completed in mere seconds to mins, depending on the complexity and size of the component being generated. Because of this, makers can accomplish high outcome rates, making plastic shot molding a suitable option for mass production
Moreover, the ability to produce large quantities continually makes certain reduced system expenses, making it a cost-efficient option for services. This production performance not just meets market demands swiftly but likewise improves the total competitiveness of makers in different sectors. Plastic injection molding remains a preferred method for high-volume production applications.
Style Adaptability
The capabilities of plastic injection molding expand beyond high production performance to include considerable layout adaptability. This production process allows designers and designers to create intricate and elaborate forms that may be challenging or difficult to accomplish with various other approaches (Plastic Injection Molding). The ability to easily adjust and customize mold and mildew layouts means that producers can swiftly react to altering market needs and introduce new item styles without substantial retooling
Additionally, plastic injection molding supports a variety of materials, consisting of various thermoplastics and thermosetting polymers. This variety makes it possible for the manufacturing of elements with distinct residential or commercial properties, such as improved stamina, lightweight attributes, or particular thermal and electrical qualities. In addition, the procedure permits the combination of multiple functions right into a solitary part, reducing the need for assembly and lessening possible factors of failure.
The precision of injection molding also makes sure that components are created with tight tolerances, boosting fit and feature. The versatility to produce small to huge batches efficiently better emphasizes its adaptability, making it a suitable option for both prototyping and massive production. On the whole, layout versatility is a keystone benefit of plastic injection molding, driving technology in many sectors.
Cost-Effectiveness
Cost-effectiveness sticks out as a significant advantage of plastic shot molding in production. This process permits the mass production of high-grade plastic elements at a relatively reduced cost per device, especially when compared to other manufacturing approaches. The effectiveness of shot molding depends on its ability to produce complex forms with minimal waste, maximizing material usage and lowering overall expenditures.
Additionally, the rate of production is an important consider cost-effectiveness. As soon as the preliminary mold is produced, the moment required to produce each subsequent component is substantially lowered, bring about increased outcome and faster turn-around times. This quick production capacity not just meets high-volume needs yet also decreases labor expenses, as automated systems can manage a lot of the process.
Additionally, the sturdiness and durability of injection-molded items add to their cost-effectiveness gradually. These elements usually need much less upkeep and substitute, resulting in lower lifecycle prices for makers and end-users alike. In recap, the cost-effectiveness of plastic injection molding makes it an attractive choice for services looking for to enhance their production performance while maintaining item quality.
Material Convenience
Material flexibility is a hallmark of plastic shot molding, allowing suppliers to choose from a wide variety of polymers that meet specific efficiency demands. This adaptability permits for the manufacturing of parts tailored to numerous applications, varying from automobile components to customer products.
Typically used products include acrylonitrile butadiene styrene (ABDOMINAL MUSCLE), polycarbonate (COMPUTER), and polypropylene (PP), each offering one-of-a-kind properties such as influence resistance, warm tolerance, and chemical security. Suppliers can choose materials based upon qualities like stamina, weight, and thermal security, guaranteeing completion product fulfills practical and visual needs.
In addition, the capacity to integrate different polymers via co-injection methods more improves material flexibility. This allows for the development of multi-layered parts with distinctive characteristics, such as soft-touch surfaces integrated with inflexible architectural aspects.
Furthermore, advancements in naturally degradable and recycled products are broadening the choices readily available, straightening with sustainability objectives in manufacturing. Generally, the diverse material options in plastic shot molding equip suppliers to introduce and enhance their products, assisting in the development of extremely specialized and competitively beneficial remedies.
Enhanced Item Sturdiness
Improved item sturdiness is just one of the significant benefits offered by plastic shot molding, as the production procedure permits accurate control over material buildings and component design. This accuracy makes sure that the last items show enhanced mechanical toughness and durability, which are important consider an array of applications, from durable goods to commercial parts.
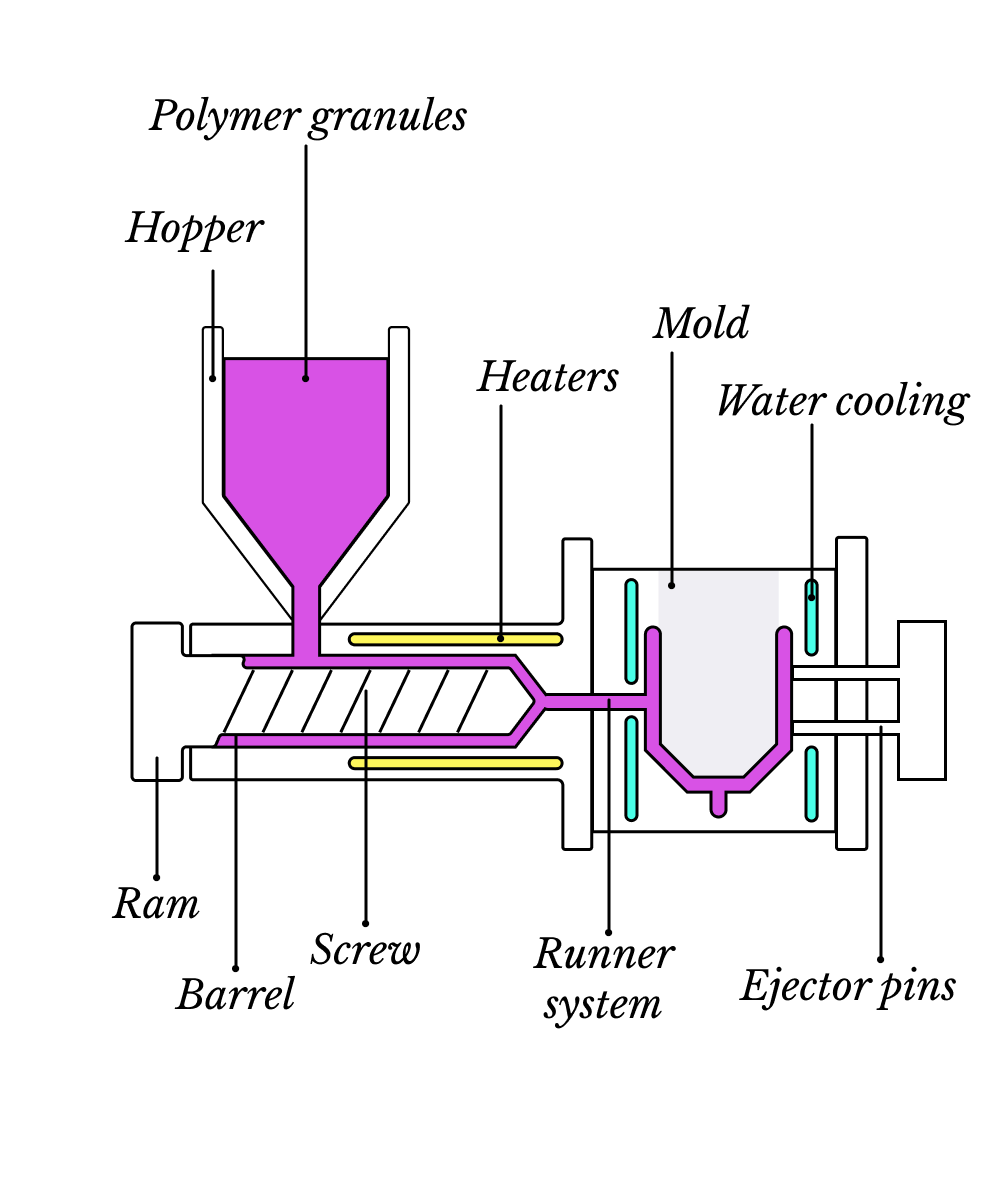
Furthermore, the complex geometries possible via injection molding enable the development of components that can hold up against tension and pressure better than traditional manufacturing techniques. The uniform wall surface thickness and lowered product waste also add to the overall stability of the product, lessening the opportunities of failure during its lifecycle.
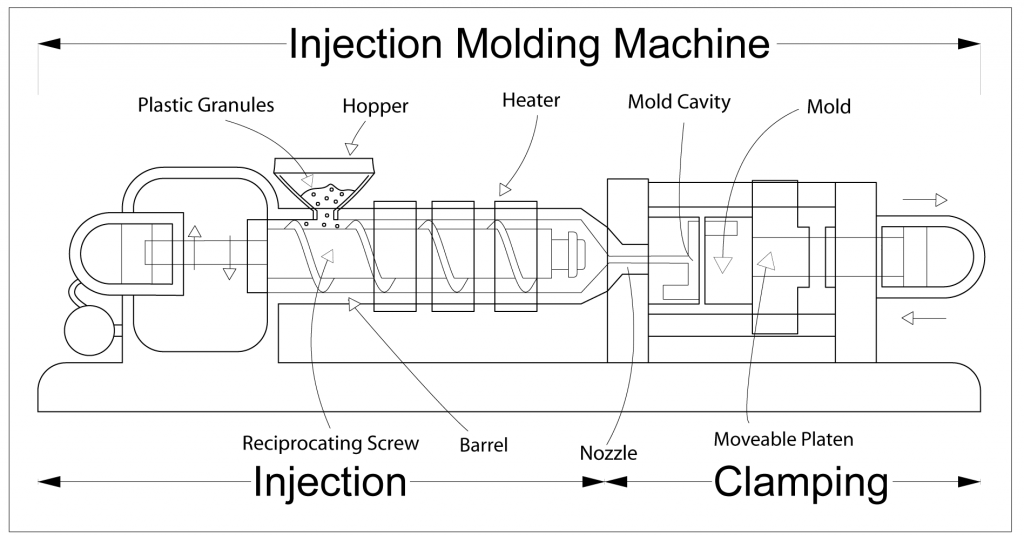
Final Thought
In final thought, plastic injection molding presents substantial advantages in production, consisting of high manufacturing performance, layout flexibility, and cost-effectiveness. These variables collectively establish plastic injection find here molding as an optimum remedy for mass production applications, resolving the dynamic needs of contemporary production settings.
Plastic shot molding has emerged as an essential strategy in the production field, offering a variety of advantages that dramatically improve production procedures.One of the most substantial benefits of plastic injection molding is its high manufacturing effectiveness, which can result in the fast production of thousands of similar components within a brief timeframe. Plastic Injection Molding.The capabilities of plastic injection molding expand beyond high manufacturing effectiveness to encompass significant style versatility.In conclusion, plastic shot molding provides substantial advantages in manufacturing, consisting of high manufacturing Check Out Your URL efficiency, layout adaptability, and cost-effectiveness. These aspects jointly develop plastic injection molding as an ideal option for mass manufacturing applications, addressing the vibrant click here for more info demands of contemporary production environments
Comments on “Enhancing Item Growth with Advanced Plastic Injection Molding Solutions”